So, consequently for our die casting component manufacturing service we of course offer our all-round carefree package to our customers as well – virtually everything „from one cast“.
The employees in our Bosnia and Herzegovina factory are truely multitalented – they cast with a lot of experience, refine the components with devotion and perfection and add colour to the game in our painting lines.
Efficient logistics channels allow us to realise projects in no time and definitely pollute the environment significantly less than comparable transports from Asia.
We are
Constructive
And know what we do, because in our engineering offices only specialists are at work.
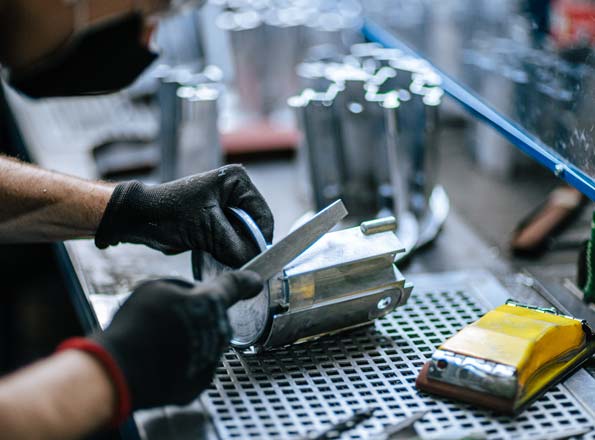
Custom-fit
We assist you in component layouts and designs which are most suitable for casting and in the construction of die casting tools, in order to assure consistently high quality and pinpoint accuracy of fit.
Self-catering
For we build all tools by ourselves in our fully equipped in-house tooling shop.
From one cast
In our production in Bosnia and Herzegovina we manufacture customised luminaire components by aluminium die casting on 5 cold chamber horizontal die casting machines from 200t up to 800t. Components with a max. weight of 10,5 kg – depending on wall thickness and fins – can be machined.
The most commonly used aluminium alloys are
Al 226 DIN EN 1706 mainly for indoor applications and
Al 231 DIN EN 1706 predominantly for outdoor products
Pedantic
at least in post-processing the cast parts and perfecting our products with devotion.
We are as accurate at that as the people with the nail scissors in the lawn … well, you know what we mean. After all, the mechanical and manual post-processing of cast parts is an art. At the end it shows what casting quality is all about.
By means of state-of-the-art CNC controlled machines we take care of the refinement of the cast parts by drilling,deburring, milling, grinding and barrel finishing.
Colorful
Of course we paint our components in our in-house painting shop.
Also when painting we are setting high quality standards: once cast and post-processed the parts receive a high precision surface pre-treatment, so that the subsequent powder coating perfectly adheres.
The Jordan group owns a fully automated powder painting plant which allows us to apply a modern industrial coating that meets the highest requirements for environmental sustainability.
Tough inspections
according to German standards, have a German quality management and are – not without reason – ISO certified in Bosnia-Herzegovina as well.
Already one hand on the receiver, just one decisive mouse click away from us or yet too flooded by so many advantages at once?
Here is a summary for all of you, who want to sleep on it:
- longstanding experience in aluminium die casting
- support in cast-friendly component layout and design, component and tooling construction to ensure consistently high quality
- high precision fit
- short transport routes due to production in Bosnia-Herzegovina
- German quality management including ISO certification
- 5 cold chamber horizontal die casting machines from 200t up to 800t
- components of up to a max. weight of 10,5kg depending on wall thickness and fins
- aluminium alloy Al 226 DIN EN 1706 indoor applications
- aluminium alloy Al 231 DIN EN 1706 outdoor products
- milling
- grinding
- barrel finishing, trowalising
- deburring
- drilling
- CNC-processing on 3 and 3 ½ -axis processing centres
- processing on CNC lathes
- surface refinement
- in-house painting lines
- surface pre-treatment with pinpoint accuracy
- powder coating – automated cleansing and drying plant with subsequent powder coating lines – Wagner spray systems manual, GEMA automated
- small quantities to large scale series
- flexibility
- in-house tooling shop
- 5-axis milling
- wire-cut EDM
- vertical EDM
- CNC turning
All in one hand to provide you everything from one source.